High-flow filters, as the name suggests, are designed to handle a larger volume of fluid or gas compared to conventional filters, offering both a high flow rate and a longer service life. Essentially, a high-flow filter is defined by its capacity to purify large volumes of water or other fluids within a short period, without compromising on the quality of filtration.
The ultimate function of a high-flow filter is to provide efficient and effective filtration at high flow rates. This is particularly important in applications where large volumes of fluid need to be processed swiftly. They are especially useful in industrial settings, such as manufacturing plants or large commercial facilities, where the demand for filtered water or fluids is high.
A key feature of these filters is their large filter area, which not only accommodates higher flow rates but also extends the filter's lifespan by delaying the onset of clogging. The high flow filters' design usually includes pleated filter media, which increases the surface area for filtration and hence aids in the high flow rate.
Another core function of high-flow filters is reducing the operating costs. Given their longer service life and minimal need for replacement, high-flow filters can be cost-effective in the long run, particularly in industrially intensive operations.
To sum it up, high-flow filters are specialized filtration systems defined by their ability to efficiently handle large volumes of fluid at fast flow rates, allowing for optimized filtration performance and cost-effective operations. They play a critical role in ensuring the purity standards in industrially intensive processes where high volume fluid management is a necessity.

The working principle of a high-flow filter is grounded in the concept of maximizing filter media surface area to accommodate a larger flow of fluid without compromising filtration efficiency.
At the core of a high-flow filter lies the filter cartridge, which is typically pleated to allow a greater surface area for filtration. This means more contaminants are caught from the fluid as it passes through, while the larger area enables a higher volume of fluid flow compared to conventional filters.
When the fluid enters the system, it is directed towards the filter cartridge. Due to the deliberate design of the pleated filter media, the fluid's path across the entire filter surface is maximized. The filter media effectively traps and retains impurities and particulates, allowing only clean fluid to flow through.
The filtration efficiency and the high flow rate of these filters are maintained through a balance between the pore sizes of the filter media and the pressure. While the pore size determines the particle size that can be filtered out, the pressure helps maintain the high flow rate. If the pore size were too small, it would hinder the flow rate, and if too large, it would compromise the filtration quality.
One notable aspect of high-flow filters is that they are usually designed for depth filtration, where multiple layers of filter media stop not just large particulates, but smaller ones as well, enhancing the overall filtration efficiency.
Ultimately, what defines a high-flow filter is not just its ability to handle large fluid volumes rapidly, but also its long service life, which reduces the time and cost associated with frequent filter changes. This comes from the use of robust, high-quality materials and innovative design features, such as pleated filter media and depth filtration.
A high-flow filter consists of several key components, each with its specific function to facilitate the filtration process.
Firstly, the filter housing acts as the outermost layer, providing a robust and secure casing for the internal components. It's typically made from industrial-grade materials to withstand varying operating conditions. The housing also contains inlets and outlets for the fluid to enter and exit.
At the center of the housing resides the filter cartridge, which is the heart of the high-flow filter. This cartridge is usually designed with pleated media. The pleats increase the effective surface area of filtration, allowing for greater quantities of fluid to be processed within a short period.
The filter cartridge's primary role is to remove impurities from the fluid. It is typically composed of a fine mesh material designed to prevent particulates of varying sizes from passing through.
The supporting core and end caps of the filter provide structure and stability to the filter cartridge. The core lends support to the pleats, ensuring they maintain their shape, even with heavy loads of particulates. The end caps seal the filter cartridge, helping to prevent leakage or bypass of unfiltered fluid.
Now, onto the function of a high-flow filter. Its primary function is, of course, to filter fluids at high flow rates efficiently. However, it's also designed to maximize service life, thereby reducing the frequency of filter changes and overall operating costs.
Through its innovative design, a high-flow filter not only assures larger volumes of fluid are treated quickly, but it also ensures superior filtration efficiency. Thanks to the spacious filter cartridge design, it can hold a significant amount of impurities before needing a replacement.
In summary, the components of a high-flow filter are designed to work together seamlessly. From the robust housing to the pleated filter cartridge and supportive core, each element contributes to its function of efficient high-volume fluid filtration over an extended service life.
The materials used in the construction of a high-flow filter cartridge play a significant role in its effectiveness and efficiency. Predominantly, these materials include:
Polypropylene (PP): This is a common material used in filter cartridges due to its excellent chemical resistance and physical durability. Polypropylene is suitable for a variety of applications due to its ability to withstand a wide range of temperatures.
Synthetic Glass Fiber: This is often chosen for its excellent filtration performance. Synthetic glass fiber cartridges are used when a very high level of purity is required. This material is characterized by a highly complex mesh-like structure that ensures high-efficiency filtration.
Both these materials are designed for deep layer filtration. The large diameter of these filters guarantees a large filtering surface area, increasing the filtration flow, and thus reducing the quantity of filters and filter housing required. They provide longer service life and high flow rates, thereby significantly saving on equipment investment costs and labor costs.
It's important to note that the selection of filter material is dependent on the application and the impurities that need to be filtered. Each material has its unique attributes and is effective at trapping specific types of contaminants. Therefore, the decision should be based on a thorough understanding of the application's demands and the contaminants in the liquid or gas being filtered.
Choosing the appropriate filter material based on application and the impurities to be filtered involves these steps:
Identify the Type of Contaminants: The choice of filter material is primarily determined by the nature of the contaminants. For instance, Polypropylene filters are excellent for filtering out larger, solid particles like sand, dust, and rust. Glass fiber filters, on the other hand, are better for eliminating smaller particles and providing a higher level of purity.
Assess the Working Conditions: The material of the filter should also be suitable for the working conditions. This includes the operating temperature, the pH of the fluid, and its chemical composition. For example, if the fluid is acidic, the filter material should have good resistance to acids.
Understand the Desired Filtration Level: Different filtration materials can filter out particles of different sizes. Knowing the maximum particle size that can be present in the filtered product will help you select the appropriate filter material.
Consider Flow Rate: The chosen material should allow for the desired flow rate. Some materials may filter out more impurities, but they may also significantly reduce the flow rate of the fluid.
Check Regulatory Requirements: If the filtration is for specific uses such as food & beverage or pharmaceutical applications, there may be regulatory requirements the filter material needs to comply with.
Cost and Lifespan: Lastly, you also need to consider the cost of the filter and its expected lifespan. While some materials might be expensive, they can also last longer and provide better performance, proving to be more cost-effective in the long run.
In conclusion, choosing the correct filtration material is a complex task that requires a comprehensive understanding of the filtration requirements, the properties of the different filtration materials, and the application's specific constraints and requirements.
High-flow filter cartridges offer numerous advantages and unique characteristics that distinguish them from other types of filtration systems. Here is a detailed breakdown:
Higher Flow Rates: As indicated by the name, high-flow filter cartridges are characterized by their ability to handle higher volumes of fluid at a faster rate, thus increasing productivity.
Greater Efficiency: The design of high-flow cartridges is set in a way that maximizes the surface area of the filter material, contributing to higher efficiency. This makes them ideal for applications where a large volume of fluid needs to be filtered quickly.
Long Service Life: High-flow cartridges typically have a higher dirt-holding capacity which prolongs the filter replacement intervals, resulting in lower maintenance costs and downtime.
Reduces Operational Costs: The large diameter and central opening of these cartridges can reduce the number of filters and filter housings required, leading to savings in equipment investment and labor costs.
Versatility: High-flow filter cartridges can be used with a broad range of liquids and gases, making them versatile for different industrial applications.
Environmentally Friendly: These filters generate less waste because of their long lifespan, making them a more environmentally friendly choice.
Quality Filtration: Despite the higher flow rates, these cartridges do not compromise on the quality of filtration. They are designed to remove a substantial amount of contaminants, ensuring the output is of high quality.
Easy Installation and Replacement: High-flow cartridges typically feature a design that allows for a quick and easy installation and replacement process, reducing labor and time spent on maintenance.
In conclusion, high-flow filter cartridges provide a superior and cost-effective solution for large-scale and high-speed filtration needs. They epitomize the balance between efficiency, quality, sustainability, and practicality in industrial filtration systems.
High-flow filter cartridges achieve efficient filtration and extended service life through a multitude of design characteristics and material innovations. Here's how:
Greater Surface Area: High-flow filters typically have a pleated design, which greatly increases the filter's surface area compared to traditional designs. This increased surface area allows for a greater volume of fluid to be filtered at once, resulting in higher efficiency and longer lifespans.
Innovative Filter Media: These filters commonly use advanced filtration mediums. For instance, some high-flow filters might use a gradient density medium, which has larger pores on the outside and progressively smaller pores toward the inside. This design maximizes contaminant capture and allows the filter to effectively filter particles of various sizes without becoming clogged quickly.
Dirt-holding Capacity: High-flow filters are designed to hold a larger quantity of particulates. This means that they don't have to be replaced as often, prolonging the service life.
Backwashing Capability: Some high-flow filters are designed to be backwashed - a method of cleaning the filter where fluid is passed in the reverse direction to dislodge trapped particles. This extends the lifespan of the filter and ensures it operates at peak efficiency for longer periods.
Constructed for Strength: High-flow filter cartridges are generally made from sturdy materials to resist wear and tear, erosion, and chemical degradation, ensuring their structural integrity under high flow rates.
Sealing Arrangements: High quality sealing arrangements prevent bypass and ensure all fluid is properly filtered, increasing operational efficiency and longevity.
By taking advantage of these design and material features, high-flow filter cartridges offer both efficiency in filtration and a longer lifespan, making them an excellent choice for a variety of industrial applications.
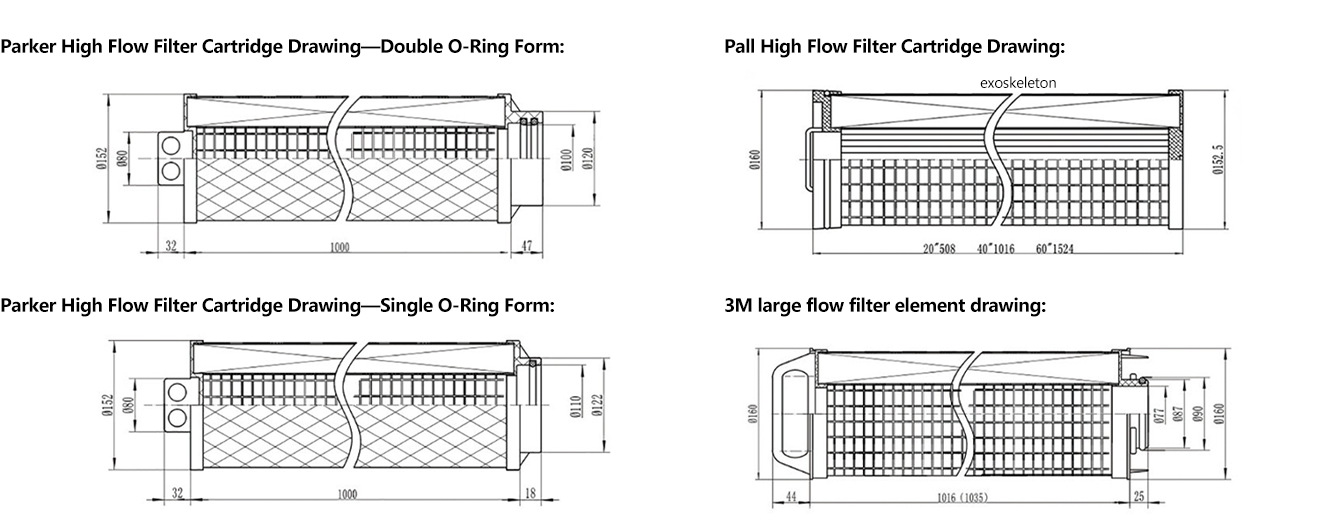
High-flow filter cartridges come in a wide array of specifications, with various parameters that meet different industrial needs. Here are some typical characteristics:
Diameter Measures: High-flow filter cartridges often have larger diameter measures, which could range from about 2.5 inches to 6 inches. The larger diameter provides higher surface area for filtration and, therefore, a higher flow rate.
Length Measures: These cartridges also come in various lengths, typically ranging from 10 inches to 40 inches. The length influences the quantity of liquid that the filter can process before requiring replacement.
Maximum Operating Temperature: This indicates the maximum heat level a cartridge can withstand during operation without suffering damage. Typically, it falls within the range of 40-80°C (104-176°F) for most high-flow cartridges, but it can vary depending on the material used.
Maximum Pressure Drop: This refers to the largest acceptable decrease in fluid pressure as it passes through the cartridge. It's usually about 0.2-0.4 bar under normal operating conditions.
Filtration Efficiency: High-flow filters often come with efficiencies upwards of 99.9%, removing very high percentages of particulate matter. This is often characterized by the filter's micron rating, indicating the smallest particle size the filter can effectively remove.
Flow Rate: The flow rate represents the volume of fluid that can pass through the filter per unit time. In high-flow cartridges, due to their large diameters, this value is often high, typically measured in gallons per minute (GPM) or cubic meters per hour (m³/h).
Material: Different high-flow cartridges are made from a variety of materials, including polypropylene, glass fiber, stainless steel, etc. The choice depends on the filtration requirement and operating conditions.
End Cap Configuration: Depending on the housing interface requirements, different end cap configurations are available, such as double open end (DOE), single open end (SOE), or threaded connections.
Application-Specific Parameters: There may be other parameters and features specific to an application, such as resistance to certain chemicals or suitability for food-contact applications.
These substantial and diverse options allow different industries to choose the most suitable high-flow filter cartridge for their specific filtration requirement. They embody the ability of these filter cartridges to adapt and serve efficiently in various environments while maintaining high performance.
High-flow filter cartridges are versatile, finding use in an array of industries due to their efficiency, high capacity, and extended service life. Here are some typical applications:
Oil and Gas Industry: High-flow filters are extensively used for processing petroleum and its derivatives. They efficiently filter impurities in crude oil, natural gas, and processed fuels. The robust construction also allows them to endure harsh operating conditions and corrosive substances typical in this sector.
Pharmaceutical Industry: Ensuring purity is vital in medicine and drug manufacturing. High-flow filters remove particulates, biological contaminants and residuals, helping meet stringent hygiene and quality standards.
Food and Beverage Industry: High-flow filters are adept at ensuring the quality of the food and beverage products by removing contaminants and optimizing taste, aroma and clarity. They may also be used in applications such as bottle washing, ingredient water treatment, and product filtration.
Water Treatment Facilities: Whether for potable water or industrial use, high-flow filters are instrumental in the initial stages of water purification to remove sediments, algae, bacteria, and viruses, rendering water safer for consumption or subsequent processing.
Chemical Industry: High-flow filters streamline chemical processing by removing unwanted particulates from basic raw materials, intermediates and finished products ensuring process integrity and product purity.
Electronics Industry: Ultra-pure water is necessary for the production of electronic components like semiconductors and printed circuit boards. High-flow filter cartridges can effectively decontaminate process water, ensuring the highest quality and reliability of electronic products.
Paints and Coatings Industry: High-flow filters improve quality in the manufacture of paints and coatings by screening out unwanted particulates and gel particles that affect the finish and performance of the products.
Power Generation: In thermal power plants, nuclear facilities, and renewable power stations, high-flow filters are used to treat water for cooling, lubrication, and other functions. This reduces wear and tear on equipment and increases overall plant efficiency.
Pulp and Paper Industry: High-flow filters facilitate the removal of contaminants, ensuring purity of the water used, and the quality of the final paper product.
In each of these industries and several others, high-flow filter cartridges enhance process efficiency, ensure product quality, and reduce costs by extending the service interval of the filter element.
High-flow filter cartridges not only exhibit superior performance, but also contribute significantly towards environmental sustainability and have a considerable societal impact. Let's delve into these aspects:
Environmental Sustainability: High-flow filter cartridges are designed to have high filtration efficiency and a large dirt holding capacity, which results in extended service life. This means less frequent cartridge replacement, leading to a reduction in waste generation. Some cartridges are even cleanable and reusable, further minimizing waste. Additionally, the improved efficiency of high-flow filters often translates into lower energy consumption in filtration processes, thus reducing the carbon footprint.
Conservation of Water Resources: In industries where water is a major component of the manufacturing process, high-flow filter cartridges can significantly reduce water usage. Their design maximizes the filtration process, reducing the amount of water wasted. This is of vital importance in regions where water is a scarce resource.
Protecting Public Health: By ensuring the purity of drinking water and the hygiene of pharmaceutical and food production, high-flow filters play an indirect, yet vital, role in protecting public health. They prevent harmful contaminants from entering consumer products, mitigating health risks.
Economic Impact: The long service life and reduced resource usage associated with high-flow filter cartridges can lead to substantial cost savings for businesses. This, in turn, could lead to lower consumer prices, job creation, and positive economic growth.
Compliance with Regulations: Stringent environmental and safety regulations in many countries require efficient filtration in various industries. High-flow cartridges help industries meet these requirements, thereby avoiding penalties and contributing to environmental safety goals.
ESLI (End-of-Service-Life Indicator): Some high-flow filters come with ESLI, a tool designed to signal the need for cartridge change, helping to avoid premature disposal and minimizing environmental impact.
Through these ways, high-flow filter cartridges weave an important narrative in environmental conservation, public health protection, economic efficiency, and regulatory compliance. They truly underpin sustainable and responsible industrial practices.