The air compressor filter element, sometimes known as the filter cartridge, is the core part of the air compressor filter system. It directly contributes to the purification of compressed air by trapping and holding the contaminants such as dust, dirt, oil, and other particulates.
Constructed from high-quality materials, the filter element is typically designed with a fine mesh or layers of filtration media. These materials are designed to be robust, able to withstand variations in pressure and temperature, while still capturing particles effectively. The precise construction and materials used may vary based on the specific needs of the application and the type of compressor system, but the primary function remains the same: to clean the incoming air.
Filter elements are often replaceable, considering that over time, the element will become filled with contaminants and its performance will degrade. The frequency of replacement depends on factors such as the air quality, level of contaminants in the environment, and the workload of the air compressor system.
Proper maintenance of the filter element not only extends the service life of the air compressor but also enhances its performance and efficiency. A clogged or dirty element can restrict airflow, resulting in loss of power, increased energy consumption, and potentially serious damage to the compressor system. Regular examination, cleaning, and timely replacement of the filter element can prevent these problems and ensure optimal operation of the air compressor.
In brief, an air compressor filter element is a critical component in maintaining the quality and efficiency of compressed air systems. It plays an indispensable role in protecting the compressor from damage and contributing to the longevity of the equipment. A well-maintained filter element is synonymous with an efficiently running compressor.

The air compressor filter element performs a fundamental task in the overall efficiency and proper functionality of an air compressor system. It delivers cleaner air by removing contaminants while allowing the system to maintain its efficiency and prolong its lifespan. Understanding the composition and functions of such a fundamental component can lead to improved operational practices and, consequently, better system performance.
Composition of Air Compressor Filter Element
An air compressor filter element typically consists of several key components:
Filter Media: This is typically the primary working part of the filter element. It could be made from different materials like cellulose, synthetic fibers, or a composite blend depending on the filtration requirements. Its purpose is to trap particles and contaminants, preventing them from entering the downstream process.
End Caps and Centre Tube: These are usually made of durable materials like metal or hard plastic, and they provide structure to the filter. The end caps hold the filter media in place, while the centre tube provides a channel for the cleaned compressed air to flow through while also serving as a support core for the filter media.
Sealing Gasket: Located on the top end cap, this rubber or silicone component seals the connection between the housing and the filter element to prevent any unfiltered air from bypassing the filter media.
Function of Air Compressor Filter Element
The filter element in an air compressor mainly has the following functions:
Particle Removal: The filter media traps and holds dust particles, dirt, and other solid contaminants present in the air before it reaches the air compressor.
Oil Aerosol Separation: Some filter elements are designed to capture tiny oil aerosols, thereby preventing oil contamination in applications where oil-free air is necessary.
Protecting Equipment: By removing contaminants before they can reach the equipment, the filter element extends the life and reliability of the air compressor and downstream equipment.
Maintaining Efficiency: A clean and high-quality filter element helps maintain the efficiency of the air compressor system by maintaining a steady airflow and minimizing energy loss due to a buildup of dirt or clogs.
To conclude, the air compressor filter element plays a vital and dual role in both protecting and enhancing the performance of the air compressor system. It's a mix of well-selected materials and design, which collaboratively work to ensure clean, contaminant-free compressed air. Therefore, choosing the right filter element and maintaining it well is indeed instrumental in the longevity and performance of an air compressor system.
An air compressor is an intricate system containing various types of filter elements, each fulfilling a unique purpose. Let's take a closer look at three key ones: the oil-gas separation filter element, air filter element, and lubricating oil filter element.
Oil-Gas Separation Filter Elements (Oil Separator Elements): These elements play a pivotal role in compressors that utilize oil in the compression process. They are designed to separate the oil from the compressed air before it leaves the system. The compressed air-oil mixture passes through the separator element, causing large oil droplets to coalesce on the filter media. These droplets then drain back into the oil sump for reuse. The result is compressed air that is almost oil-free. These types of filter elements are essential in ensuring the efficient operation of the compressor, reducing oil consumption, and delivering clean, high-quality air downstream.
Air Filter Elements: Probably the most common type of filter element, air filter elements' job is to remove particulate matter such as dust, pollen, and other airborne solids from the intake air before it enters the compressor. This is a critical function in preventing the entry of contaminants that might damage internal compressor components. Filters typically consist of pleated paper or synthetic media capable of trapping these particles. A well-functioning air filter element can significantly prolong the lifespan of the compressor, improve efficiency, and contribute to cleaner output air.
Lubricating Oil Filter Elements: As part of an oil-lubricated compressor system, these filter elements work to filter the lubricating oil itself. They remove any contaminants - particles of metal, dust, and so on - present in the oil that could potentially cause damage and breakdown of components within the compressor. Furthermore, they also ensure the quality of the oil so that it can efficiently lubricate the moving parts, reducing wear and tear and extending compressor durability as a result.
Each of these filter elements plays a vital role in ensuring the high-quality output of the compressor, which in turn depends heavily on the performance of these filters. The selection of the right filter elements, therefore, is a significant factor that affects the efficiency, operation, and longevity of the air compressor system.
Certainly, let's take a deep dive into the working principle of air compressor filter elements.
An air compressor is a complex piece of equipment that operates in a multi-stage process to pressurize air. One integral part of this machinery is its filter element, which works to remove contaminants from the air during various stages. There are several types of filter elements, including the air filter element, oil-gas separation filter element, and lubricating oil filter element, each working in a unique way:
Air Filter Element: This filter operates on a relatively straightforward principle of physical filtration. As the ambient air gets sucked into the compressor, it first needs to pass through this air filter. The filter's media, which could be made of pleated paper, synthetic material, or even a blend of the two, traps the contaminants such as dust, pollen, and other airborne particles. The cleaner air then enters the compressor for the compression process.
Oil-Gas Separation Filter Element (Oil Separator Element): Following air compression in an oil-injected compressor, the output is a high-pressure mixture of compressed air and oil. This mixture then flows into the oil separator. Inside this component, the oil-gas separation filter element exists. It's usually a deep pleated, wrapped, or staged filter that traps the oil mist. As the mist coalesces on the element's media, it condenses into larger droplets that are then returned to the oil sump due to gravitational force or existing pressure differentials. The result is cleaner, virtually oil-free compressed air that continues through the system.
Lubricating Oil Filter Element: The working principle of this filter is quite similar to the air filter element. However, instead of cleaning the intake air, it cleans the lubricant oil in an oil-lubricated compressor before it's used to cool and lubricate the system. The element traps any contaminants that could cause damage, ensuring the lubricating oil's purity before it circulates through the compressor once again.
In summary, the filter elements in an air compressor operate on the basic principle of trapping or separating impurities from the air or oil. Although the specifics might differ depending on the type of filter element and the compressor system, the overall goal remains the same - to protect the compressor's integrity, ensure efficient operation, and guarantee the quality of the output air.
Sure, let's discuss the specifications and parameters that are relevant to the filter elements in an air compressor.
Specification by Size: The filter element's size dimensions, such as diameter and height, are critical as they need to match the housing or casing of the specific compressor model. Manufacturers typically provide a code or reference number for each filter element that corresponds to certain measurements.
For instance, filter elements' diameters can range widely, from a few millimeters for small devices, to hundreds of millimeters for industrial-grade machinery. The height of the filter element can also vary accordingly.
Media Material: The material of which the filter media is made can also vary, such as cellulose, synthetic, or a mix of both, depending on the filtration needs.
Filtration Efficiency: This parameter represents the filter's ability to remove contaminants of a specific size. It's typically presented as a percentage and based on the size of the particles it's capable of filtering out.
Air Flow Rate: A filter must be able to handle the compressor's airflow rate, usually measured in cubic feet per minute (CFM). This spec ensures the filter won't restrict air to a point where it affects the compressor's performance.
Service Life: This outlines the expected lifespan of a filter, subject to operating conditions and maintenance. Often provided in hours of use, it gives an indication of when the filter will need to be replaced.
Differential Pressure: As the filter element traps particles, this causes a pressure drop across the element. High-performance filters have a low initial pressure drop and can sustain this over a longer period, resulting in energy savings.
Air Quality Class: This refers to the ISO standards the filter meets for the number and size of particles it can remove, as well as its ability to remove water and oil.
These specifications and parameters can vary greatly across different models and applications, and it's important to check them thoroughly before purchasing a new filter or replacing an existing one. Consulting the compressor's manual or the filter manufacturer is usually the best way to ensure you're choosing the correct filter elements.
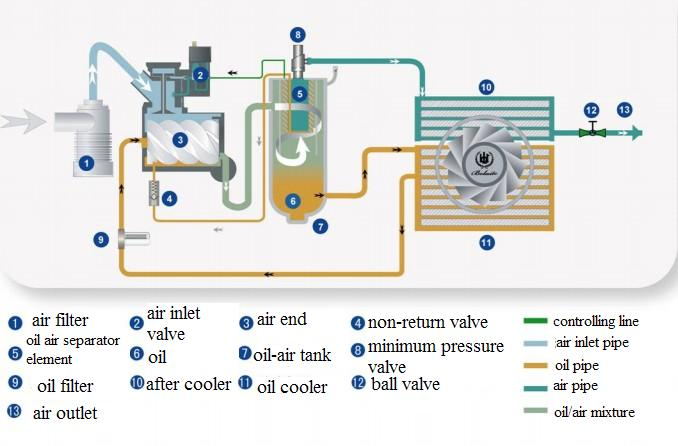
Certainly, air compressor filter elements play a crucial role in maintaining the efficiency and durability of the machinery. Let's explore the various advantages of these components:
Enhanced System Efficiency: One of the most significant advantages of filter elements is their ability to increase a compressor’s efficiency. As these filters ensure only clean air enters and leaves the compressor, they help prevent the potential damage caused by contaminant particles, thereby reducing downtime and promoting efficient operation.
Extended Equipment Life: By eliminating harmful particles from the cycling air and oil, filters protect the internal components of the compressor, preventing undue wear and tear. This extends the compressor's overall service life and reliability. This can lower total cost over the compressor’s lifespan due to fewer breakdowns and reduced maintenance needs.
Improved Air Quality: Particularly in industries where the purity of compressed air is paramount - such as in food, pharmaceutical, or high-tech industries - high-quality filter elements are vital. They secure the quality of the output air by removing oil, dust, and other fragments, providing clean, safe air that meets industry standards.
Energy Saving: A filter element that is designed to have a low differential pressure is energy efficient, as it requires less power to push air through the filter.
Minimized Oil Consumption: In oil-lubricated compressors, oil separation filter elements significantly reduce oil carry-over, ensuring minimal oil wastage and cost saving over the long term.
Flexible Usage: Due to the wide range of types, sizes, and specifications available, filter elements can be adapted to fit a variety of compressor types and applications, from small residential units to large industrial compressors.
In summary, air compressor filter elements are essential in protecting your machinery, ensuring its efficient operation and delivering uncompromised air quality. Choosing the right one for your specific needs can bring about substantial long-term benefits.
Certainly, filter elements play an integral role in maintaining and improving the operating efficiency of an air compressor. Here's how:
Minimizing Damages: Filter elements help trap and remove contaminants, such as dust, dirt, and oil particles within the air being compressed. By doing so, they prevent these damaging particles from entering the system and causing damage to internal components of the air compressor, such as the valves and seals.
Preserving Air Quality: High-quality filter elements will ensure that the output air is clean and free from impurities. This can directly impact the quality of work when using the compressed air for applications that require pure air, such as painting, food processing, or medical equipment.
Reducing Energy Consumption: A clogged or malfunctioning filter forces the compressor to work harder, consuming more power and reducing its efficiency. Regular maintenance and replacement of filter elements ensure that your compressor operates at its most efficient state, optimizing energy use.
Preventing Downtime: With a properly functioning filter element, you can avoid unwanted system shutdowns or frequent maintenance sessions which can be costly and disruptive. This ensures the compressor is working at peak efficiency for longer periods.
Extending Lifespan: When contaminants are effectively filtered out, the wear and tear of the compressor components are reduced, ensuring that the system remains efficient over a more extended period, thus prolonging its lifespan.
Ensuring Lubricant Quality: For oil-lubricated compressors, the quality of the lubricant directly affects the compressor's performance and efficiency. Oil filters keep the oil free from debris which could otherwise cause damage and reduce operational efficiency.
In conclusion, considering these benefits, regular maintenance and the use of high-quality filter elements can greatly enhance the efficiency of your air compressor, making it an essential component of the system.
Sure, air compressor filter elements are universally adopted across numerous industries due to their ability to ensure the efficiency, longevity, and safety of air compressors. Let's explore the applications across different fields:
Manufacturing: In manufacturing industries, air compressor filters are used to ensure the quality and efficiency of various applications, such as CNC machining, injection molding, sandblasting and painting. They ensure clean and dry air supply, eliminating the risk of product contamination.
Automotive Industry: Compressed air is widely used in auto manufacturing for tools, robotic assembly, painting, and finishing. A quality filter prevents dust and oil from causing imperfections in paint jobs or damages to the pneumatic tools.
Healthcare & Pharmaceutical: In these sectors, it is of utmost importance to maintain sterile and clean environments. Compressed air is often employed in operating critical instruments, ventilation systems, or manufacturing medicines. Filters play an integral role in ensuring the purity of the air used, safeguarding patient health and maintaining compliance with stringent regulations.
Food & Beverage Industry: Compressed air is used in various stages of food and beverage processing, from powering machinery, dispensing products, packaging, to maintaining a controlled environment. As contact with any contaminants can lead to spoiled products, the use of filter elements is highly essential for maintaining food and beverage quality and safety.
Construction: Air compressors are integral part of many construction systems, from powering pneumatic tools to painting and sandblasting. Clean, dry air supplied by a well-maintained filtration system can prolong the life of these tools and ensure a quality finish on construction works.
Energy Sector: In the energy industry, compressed air is used in many operations, such as in power plants for instrument air systems, in the oil and gas industry for drilling and pipe cleaning, or in wind turbines for brake systems. Filter elements in these applications ensure reliable, efficient operation and prolong equipment service life.
In summary, air compressor filter elements are widely applied across diverse industries, protecting equipment, improving efficiency, and safeguarding product and air quality. Their functionality makes them a versatile and indispensable part of many industrial processes.
Certainly, the installation and maintenance of air compressor filter elements are vital for the overall functioning and lifespan of the air compressor. The following steps will guide you with the process:
Installation:
Inspect New Filter: Before installation, be sure the new filter is clean, undamaged, and matches the specifications of your air compressor.
Turn Off the Air Compressor: It is essential for safety reasons to turn off and unplug the compressor before starting the installation.
Depressurize: Open the drain valve and let any pressurized air escape. Once the pressure gauge reads zero, you can proceed.
Replace the Air Filter: Unscrew or unclamp the old filter housing and remove the spent filter. Replace it with the new filter and securely reassemble the housing.
Check for Leaks: Turn on the compressor, allow it to pressurize, and check for any leaks. If found, immediately turn off the compressor, depressurize, and recheck your installation.
Maintenance:
Regular Inspection: Regularly check the condition of the filter element to ensure it is working properly. Look for any signs of damage or excessive dust and dirt build-up.
Cleaning: Some filters can be cleaned using a blower. If dust and dirt have accumulated on it, clean it carefully without damaging the filter material.
Replacement: Air compressor filter elements should be replaced over time as they wear out. The replacement frequency will depend on the specific operating circumstances, but a good rule of thumb is to replace them every 2000 hours or every three months.
Avoiding Environment with High Dust: Try to situate your air compressor in a location less exposed to dust and other airborne particles, if possible. This will reduce the strain on your filter elements.
Keep Track of Changes: Monitor any changes in the air compressor’s effectiveness. If you notice a drop in pressure or increase in energy usage, it could be time to replace your filter element.
The health of your air compressor depends heavily on the health of its filter elements. Regular maintenance, appropriate care, and timely replacements of your air compressor's filter elements ensure smooth functioning and longevity of the air compressor system.
Sure, the environmental impact and social implications of air compressor filter elements are significant, specifically in terms of sustainability and pollution prevention.
Environmental Impact
Energy Efficiency: Efficient filter elements can increase the operational efficiency of an air compressor. A well-maintained filter reduces energy consumption, contributing to a lower carbon footprint.
Preventing Air Pollution: By trapping harmful substances like dust particles, oil aerosols, and moisture, air filters ensure the output air is clean, preventing pollution of the work environment and contributing to the overall air quality.
Waste Reduction: The lifespan of filter elements with proper maintenance is considerable. This reduces the need for frequent replacement and resultant waste.
Recyclability: Some filter elements are created from materials that can be recycled, further reducing their environmental impact.
Social Impact
Worker Health: Clean air is crucial to maintaining a healthy work environment. Easy-to-maintain and efficient filters ensure the well-being of employees, reducing the risk of respiratory illnesses associated with polluted air.
Product Quality: Ensuring a clean-air supply in facilities substantially improves the quality of the end product. This directly benefits consumers, particularly in industries like food and beverage, pharmaceuticals, or electronics.
Socio-Economic Value: Beyond the direct use, jobs created in the manufacture, installation, maintenance, and disposal of filter elements contribute to economic growth and development.
In conclusion, improving the efficiency and sustainability of air compressor filter element systems can significantly contribute to conserving resources, decreasing pollution, protecting human health, and creating social value. They symbolize behind-the-scenes heroes, making a vital difference in environmental protection and social development.